As you clean, sharpen, and lubricate your woodworking tools, you’re not just prolonging their life; you’re ensuring your own safety and maintaining the quality of your work.
It’s crucial to follow these steps diligently, as neglecting them can lead to premature wear and tear, and potentially hazardous situations.
However, these practices are just the tip of the iceberg when it comes to tool maintenance.
To discover the comprehensive techniques that will keep your tools in top condition for years to come, and why each step is vital, you’ll want to explore further.
Contents
Clean Regularly
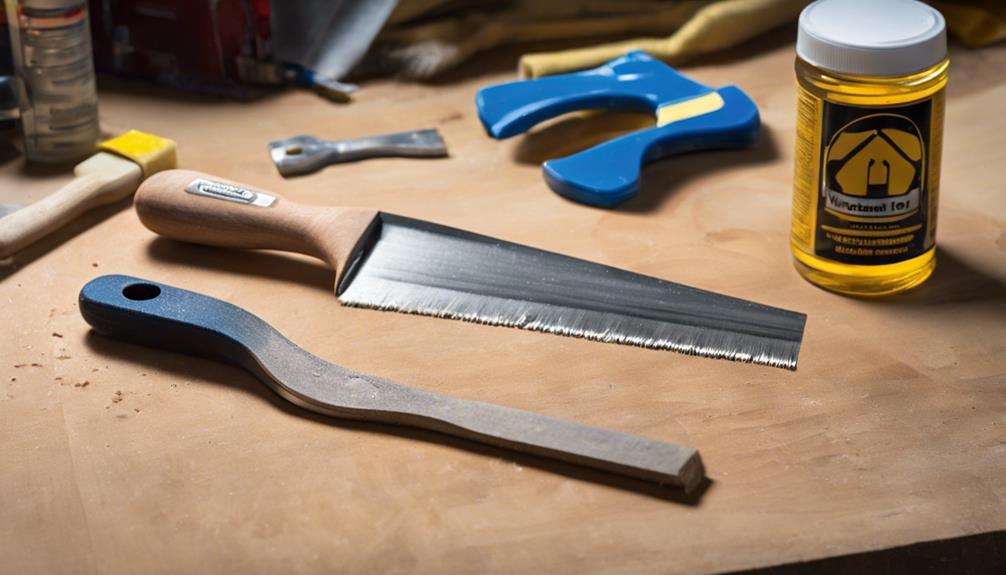
To ensure your woodworking tools maintain their efficiency and longevity, it’s crucial to clean them regularly.
Use mild soap and water after each use to prevent rust, and corrosion, and ensure optimal performance. This regular maintenance step removes debris, sawdust, and potential contaminants that could impair their function.
When cleaning, pay close attention to moving parts and air vents to prevent overheating and premature failure of power tools. Drying them thoroughly after washing is equally important to avoid moisture buildup, which can lead to rust.
Implementing a disciplined cleaning routine after each project not only safeguards your tools’ efficiency but also contributes to safety, ensuring they’re in prime condition for your next woodworking venture. Remember, meticulous care is the backbone of maintaining top-notch performance and extending the lifespan of your woodworking arsenal.
Sharpen Blades Often
Why should you consider sharpening your woodworking blades frequently? Regular maintenance ensures peak cutting efficiency and precision, crucial for any woodworking project.
Sharpening your blades often isn’t just about keeping them functional; it’s about ensuring safety, accuracy, and longevity of your tools. Here are key points to remember:
- Sharp blades reduce the risk of accidents by requiring less force.
- Proper sharpening techniques prevent damage and ensure precise cuts.
- Quality circular saw blades lead to smoother finishes.
- Regular sharpening extends the lifespan of your blades.
- Companies like Freud offer cost-effective solutions for maintaining sharpness.
Maintaining sharpened blades elevates your woodworking tasks, offering unmatched cutting efficiency and precision. Don’t overlook this critical aspect of tool maintenance; it’s fundamental for achieving professional-grade results in your projects.
Prevent Rust Proactively

Woodworkers’ worst enemy, rust, can significantly compromise the integrity of your tools by causing irreversible corrosion on metal surfaces. To keep your tools in top condition, proactive maintenance is crucial.
Moisture and air exposure are rust’s allies, speeding up the corrosion process. To combat this, you must regularly clean and thoroughly dry your tools after each use. This simple step is your first line of defense against rust formation.
Further, applying rust protectants or inhibitors can form a protective barrier, ensuring your tools’ longevity and performance. These products are specially designed to prevent rust and should be a staple in your maintenance routine. By adopting these practices, you’re not just maintaining your tools; you’re investing in their future, ensuring they remain rust-free and reliable for years to come.
Proper Tool Storage
After addressing the battle against rust with proactive measures, let’s focus on another crucial aspect of tool maintenance: ensuring your woodworking tools are stored correctly to prevent any form of damage.
- Store woodworking tools in a dry, climate-controlled environment to fend off rust and corrosion.
- Utilize cases or cabinets for storage to keep dust and debris at bay, safeguarding your tools.
- Avoid damp areas when storing power tools to protect their vital electrical components from moisture damage.
- Embrace proper storage practices to maintain the quality and longevity of your tools, ensuring peak tool performance.
- Protect your tools from moisture by choosing a dry storage location, key in maintaining their condition and functionality.
Adhering to these guidelines ensures your tools receive the proper care they deserve, enhancing their performance and extending their lifespan.
Lubricate Moving Parts
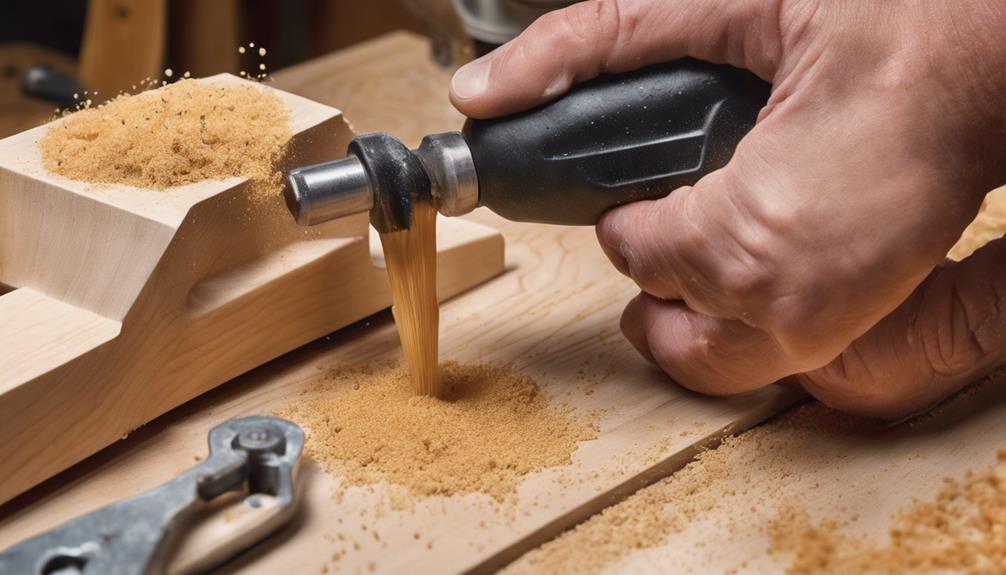
Now, let’s tackle the essentials of lubricating your woodworking tools’ moving parts.
Selecting the right lubricant is foundational, as it directly impacts the tool’s performance and durability; this choice should align with the manufacturer’s specifications.
Understanding lubrication frequency and techniques enhances tool efficiency, while being mindful of common lubrication mistakes can save you from unnecessary repairs and downtime.
Choosing the Right Lubricant
To ensure your woodworking tools operate at peak efficiency, choosing the right lubricant for moving parts is crucial. The longevity and performance of both metal and non-metal parts in your equipment heavily depend on this choice. Here’s a detailed guide to selecting the appropriate lubricant:
- Use lithium grease for bearings and metal parts to prevent corrosion and ensure smooth operation.
- Silicone spray is suitable for non-metal parts like plastic or rubber, maintaining flexibility and preventing cracking.
- White lithium grease is ideal for general lubrication needs, offering long-lasting protection.
- Teflon-based lubricants excel in reducing friction on sliding surfaces such as table saw fences, enhancing accuracy.
- Regular lubrication with the right lubricant prevents wear, reduces friction, and significantly extends the lifespan of your tools.
Lubrication Frequency and Techniques
Ensuring your woodworking tools remain in optimal condition requires lubricating moving parts every 40 hours of usage to prevent undue wear and maintain efficiency. Adhering to this lubrication frequency is pivotal for the seamless operation of your equipment.
Delving into the technical specifics, proper lubrication reduces friction in bearings, significantly enhancing the longevity and performance of your tools. It’s imperative to consult the manufacturer guidelines for both lubrication frequency and techniques to ensure you’re not only applying the correct lubricant but also employing the best methods for application.
Regular lubrication safeguards against chafing, corrosion, and overheating, thereby contributing to the overall efficiency of your woodworking tools. This practice is a cost-effective strategy to extend their lifespan and guarantee optimal functionality.
Common Lubrication Mistakes
While lubricating your woodworking tools is crucial for their upkeep, common mistakes like over-lubrication or using an incorrect lubricant type can significantly hinder their performance and durability. Here are key maintenance tips to avoid these pitfalls:
- Avoid over-lubrication: Excess lubricant attracts dust and debris, leading to clogs and damage.
- Select the right lubricant: Using the wrong type can degrade materials and impair tool function.
- Adhere to manufacturer guidelines: Always follow recommended lubrication frequencies and types for optimal tool maintenance.
- Beware of under-lubrication: Insufficient lubrication increases friction and heat, risking efficiency and safety.
- Regular checks: Periodically assess lubrication levels to prevent wear and ensure longevity.
Inspect and Replace Worn Components
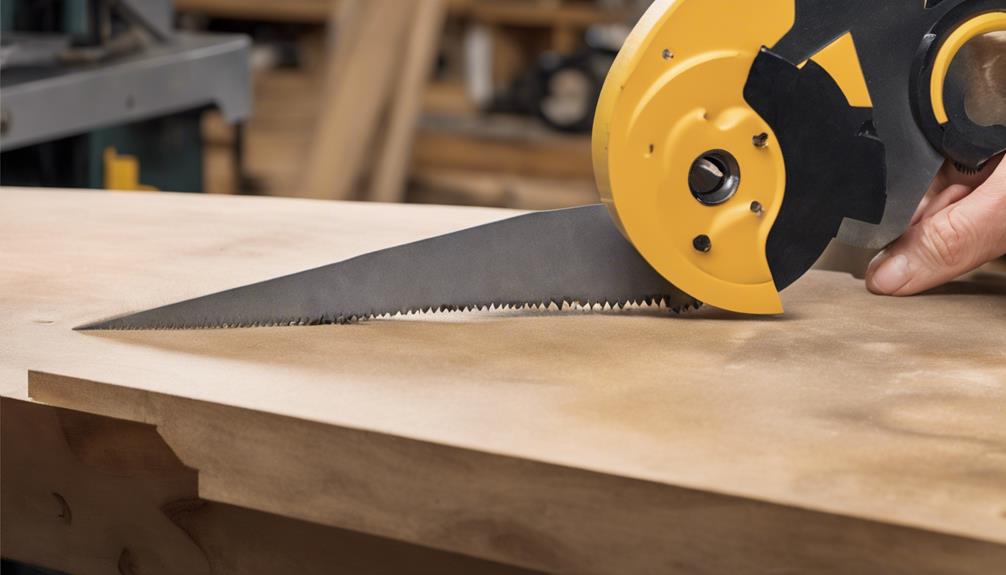
Regular inspection of components like carbon brushes and drive belts is crucial for maintaining your tool’s peak performance and safety. To ensure optimal tool performance and extend tool lifespan, it’s essential to inspect worn components and replace worn parts promptly. This not only prevents electrical conduction issues but also maintains tool functionality, avoiding safety hazards.
Component | Signs of Wear | Action |
---|---|---|
Carbon Brushes | Uneven wear, sparks | Replace |
Drive Belts | Cracks, fraying | Replace |
Bearings | Noise, vibration | Replace |
Timely replacement of components like bearings and blades is critical to prevent damage and breakdowns. Monitoring and replacing worn components is a proactive step in preventing costly repairs and maintaining tool efficiency. This practice is a cornerstone of effective woodworking tool maintenance.
Align and Calibrate Precision Tools
To ensure your woodworking projects meet professional standards, it’s vital you regularly calibrate your precision tools, such as table saws. This process not only boosts your safety and efficiency but also significantly enhances the accuracy of your cuts.
Incorporating aftermarket rip fences can further refine tool alignment, elevating your project outcomes to new heights of precision.
Importance of Regular Calibration
Ensuring your precision tools undergo regular calibration is crucial for maintaining their accuracy and ensuring safe operations. This maintenance step is as vital as regular cleaning and must be part of your routine to preserve tool functionality. Precision tools require regular calibration to prevent errors and enhance your projects’ quality. Always refer to the owner’s manual to understand the frequency and procedure for calibration.
- Follow calibration guidelines to maintain accuracy.
- Recalibrate tools after a specified number of usage hours.
- Proper alignment prevents errors in cuts.
- Manufacturers offer professional calibration services.
- Ensuring reliable tool performance through precision.
Adhering to these principles ensures your tools remain in top condition, contributing to safer, more efficient, and higher-quality woodworking projects.
Achieving Optimal Tool Performance
Achieving optimal performance from your precision tools necessitates diligent alignment and calibration, ensuring your woodworking projects meet the highest standards of accuracy and quality. Regular alignment checks, particularly for table saws, are fundamental to guarantee precise cuts.
This precision directly impacts the outcome of your projects. Proper calibration of these instruments isn’t just about maintaining consistency; it’s about elevating your work to professional levels.
Consider incorporating aftermarket rip fences to boost the accuracy of your tools further, enhancing the overall quality of your projects.
Well-aligned tools significantly reduce the risk of errors, ensuring your power tools keep running smoothly, especially in complex woodworking tasks. By committing to regular calibration and alignment, you’re not just optimizing performance but also extending the lifespan and efficiency of your precision woodworking tools.
Conclusion
In wrapping up, remember, that your woodworking tools demand consistent care. Regularly clean and sharpen them to maintain peak performance. Don’t overlook rust prevention; it’s crucial.
Store your tools correctly to avoid unnecessary wear. Lubrication keeps moving parts functioning smoothly, so don’t skimp on it. Vigilantly inspect and replace any components showing wear to avoid mishaps.
Lastly, precise alignment and calibration are non-negotiable for accurate work. Adhering to these practices ensures your tools remain in top shape, maximizing both longevity and efficiency.